Top 12 Industrial automation trends for 2025
Explore the top 12 industrial automation trends for 2025, featuring real-world use cases from Siemens, ABB, Rockwell, and more. Discover how AI, 5G, IIoT, and digital twins are shaping the future of smart manufacturing
4/23/20256 min read
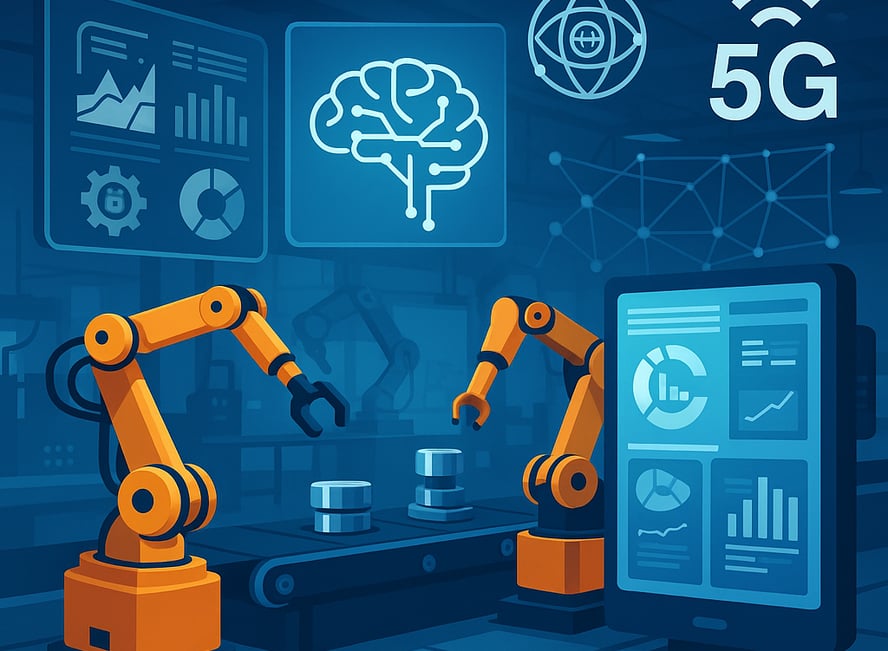
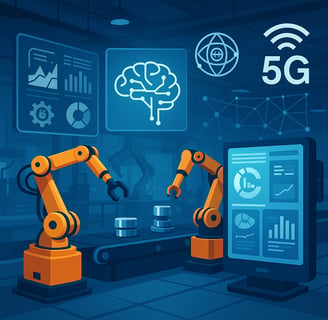
Top 12 Industrial Automation Trends for 2025
As we enter 2025, the industrial automation landscape is rapidly transforming, driven by emerging technologies, shifting labor dynamics, and the demand for greater operational efficiency. From AI-driven control systems to cyber-physical integration, this year is set to redefine what’s possible in smart manufacturing.
The future of manufacturing is here — and it’s intelligent, connected, and rapidly evolving. In this post, we dive into the top 12 industrial automation trends for 2025, highlighting real-world examples from global leaders like Siemens, ABB, Rockwell Automation, and Schneider Electric. From AI-powered maintenance to sustainable automation and low-code platforms, these trends are not only transforming industry — they’re redefining how we interact with technology, optimize production, and create a more efficient, inclusive, and sustainable world.
1. AI-Powered Predictive Maintenance
Artificial Intelligence (AI) is now at the heart of predictive maintenance strategies revolutionizing predictive maintenance, quality control, and process optimization. By analyzing equipment performance data in real time, AI systems can anticipate failures before they happen, reducing downtime and saving costs. While most cases represents still predictive capabilities, Gartner predicts that 33% of enterprise software will include agentic AI by 2028, enabling autonomous decision-making.
✅ Why it matters: Increases equipment lifespan and productivity
📈 Trend Insight: Adoption rates of AI in manufacturing are projected to grow 40% year-over-year in 2025.
💡 Use Case: Siemens MindSphere with AI Analytics
Technology: Siemens MindSphere + AI modules
Application: In automotive manufacturing, predictive analytics detect anomalies in robot arm vibrations.
Impact: Reduces unplanned downtime by up to 30%, and enhances worker safety by flagging risks before failure.
Social Value: Keeps manufacturing efficient and sustainable, preventing waste and conserving energy.
2. Integration of 5G in Industrial Networks
The implementation of 5G technology in factories enables ultra-fast, low-latency communication between machines, sensors, and cloud platforms, paving the way for real-time control and IoT integration. Companies like Siemens and Phoenix Contact are deploying private 5G networks to enhance machine-to-machine connectivity and support data-intensive applications like AR/VR.
✅ Why it matters: Real-time data transmission without delay
🔍 Use Case: Smart factories using 5G to power autonomous vehicles and remote operations.
💡 Use Case: Ericsson + ABB Smart Factory in Sweden
Technology: ABB robots + Ericsson 5G infrastructure
Application: Real-time robotic welding control and remote quality inspection using HD video streams.
Impact: Enables ultra-low latency (<1ms) communication and cloud robotics.
Social Value: Promotes decentralized production, making factories more resilient to disruptions.
3. Rise of Edge Computing
Edge computing allows data processing to happen closer to the source — on the factory floor — reducing reliance on centralized cloud systems. Edge computing processes data locally for low-latency responses, while cloud computing supports scalable analytics and storage. Manufacturers are adopting hybrid models: edge devices handle real-time control (e.g., Phoenix Contact’s PLCnext), while cloud platforms like DeepBrainz Technologies centralize data management.
✅ Why it matters: Lower latency, better data security, and faster decisions
🔧 Example: Real-time quality control using local AI algorithms
💡 Use Case: HPE Edgeline Converged Edge Systems + Rockwell Automation
Technology: HPE Edgeline + Rockwell's FactoryTalk Edge Gateway
Application: Real-time defect detection in packaging lines without relying on cloud latency.
Impact: 40% faster response times in quality control loops.
Social Value: Reduces waste, improves quality, and minimizes reliance on bandwidth-heavy cloud systems.
4. Human-Robot Collaboration (Cobots)
Collaborative robots, or cobots, are becoming more sophisticated and are now safely working side by side with humans in complex tasks. Cobots work alongside humans in tasks like assembly and material handling, improving safety and productivity. Mobile robots (AMRs) from companies like Botshare automate logistics, while self-healing robots reduce maintenance needs. The global robotics market is projected to reach $52.7 billion by 2033
✅ Why it matters: Enhances productivity and worker safety
🛠️ Industries impacted: Electronics, automotive, and small-scale manufacturing
💡 Use Case: Universal Robots (UR10e) + OnRobot Grippers
Technology: UR cobots + adaptive grippers
Application: Electronics manufacturers using cobots for delicate circuit board handling.
Impact: Productivity boost with reduced ergonomic injuries in humans.
Social Value: Job enrichment, not replacement — safer and more inclusive workplaces.
5. Industrial IoT (IIoT) Going Mainstream
IIoT devices are now more accessible and widely adopted. Sensors connected via IoT are gathering actionable data across production lines. IIoT connects machines, sensors, and systems to enable real-time monitoring and data-driven insights. This trend improves predictive maintenance, resource optimization, and supply chain transparency. Companies like VISUALYS offer customizable IIoT platforms for live data tracking, while Rockwell Automation emphasizes IIoT as foundational to smart factories
✅ Why it matters: Enables real-time monitoring, energy management, and process optimization
🌐 Expected Growth: Over 30 billion connected IIoT devices by 2030.
💡 Use Case: Schneider Electric’s EcoStruxure Platform
Technology: EcoStruxure + connected sensors + mobile apps
Application: Smart energy monitoring across multiple global facilities.
Impact: Achieved 25% energy savings through connected insights.
Social Value: Enables large corporations to achieve their net-zero goals.
6. Digital Twins for Real-Time Simulation
A digital twin is a virtual model of a physical asset. It allows manufacturers to simulate and test operations before applying them in the real world. Virtual replicas of physical systems allow simulation and optimization. For example, Siemens uses digital twins to validate machine configurations, reducing development costs. These tools also support sustainability initiatives by optimizing energy use.
✅ Why it matters: Reduces error, cost, and time to market
🔁 Popular in: Aerospace, automotive, and process industries.
💡 Use Case: Siemens NX + Digital Twin for Machine Tools
Technology: Siemens NX + Teamcenter + Simcenter
Application: Aerospace companies simulate jet engine assembly digitally before real-world execution.
Impact: Cut development time by 40%, reduced errors, and enhanced innovation.
Social Value: Promotes safer, more efficient technologies in critical industries.
7. Cybersecurity for Industrial Control Systems
As automation becomes more connected, cybersecurity is critical. OT (Operational Technology) security is now a top priority for companies investing in smart systems. With increased connectivity, protecting industrial systems from cyber threats is critical. Solutions include AI-driven threat detection, blockchain for secure data sharing, and compliance with standards like IEC 62443. Rockwell Automation and Phoenix Contact highlight cybersecurity as a frontline priority.
✅ Why it matters: Protects against cyberattacks on industrial infrastructure
🧠 2025 Insight: ISA/IEC 62443 standards are becoming industry norms.
💡 Use Case: Fortinet OT Security + Honeywell Experion DCS
Technology: Fortinet FortiGate NGFWs + Honeywell control networks
Application: Real-time intrusion detection for critical infrastructure (e.g., energy plants).
Impact: Blocks cyberattacks that could halt national-level energy supply.
Social Value: Protects essential services from growing cyber threats.
8. Advanced SCADA & HMI Systems
SCADA (Supervisory Control and Data Acquisition) systems are evolving with better user interfaces, real-time analytics, and cloud-based dashboards.
✅ Why it matters: Improves decision-making and operator efficiency
🖥️ Trend: AI-integrated SCADA platforms are gaining popularity
💡 Use Case: GE Digital iFIX HMI/SCADA + Predix Platform
Technology: iFIX + AI analytics from GE Predix
Application: Real-time visualization of performance metrics in a food processing plant.
Impact: Reduced batch rejections and increased compliance with food safety.
Social Value: Enhances public health by ensuring higher standards in food production.
9. Sustainable Automation Solutions
Eco-efficiency is now a priority. Automation technologies are being designed with sustainability in mind — from energy-efficient robots to waste-minimizing control systems. Manufacturers are prioritizing energy-efficient motors, renewable energy integration, and circular economy practices. Schneider Electric’s AI-driven recycling solutions and Tesla’s Gigafactory exemplify efforts to reduce carbon footprints.
✅ Why it matters: Reduces carbon footprint while lowering operating costs
🌱 Buzzword: “Green Automation”
Use Case: ABB’s Energy-Efficient Drives + Smart Motors
Technology: ABB ACS880 Drives + IE5 SynRM motors
Application: Paper mills reducing motor power consumption across multiple conveyors.
Impact: 50% less energy usage in critical systems.
Social Value: Major contributor to lowering CO₂ emissions in heavy industry.
10. Low-Code/No-Code Automation Tools
Low-code platforms are democratizing automation by allowing non-technical staff to create workflows and control systems without deep programming knowledge.
✅ Why it matters: Accelerates deployment and improves flexibility
⚡ 2025 Highlight: A surge in adoption across small and mid-size manufacturers
💡 Use Case: Siemens Mendix + Industrial Edge App Development
Technology: Mendix + Siemens Industrial Edge platform
Application: Operators design custom dashboards and workflows for packaging control without coding.
Impact: 3x faster deployment of digital solutions.
Social Value: Empowers non-programmers to drive digital transformation on the factory floor.
11. Immersive Technologies (AR/VR).
AR/VR tools enhance worker training, maintenance, and design. For instance, jungle VR’s software detects design errors in virtual factories, while Rockwell Automation’s Vuforia AR aids equipment troubleshooting.
✅ Why it matters: accelerates training and remote collaboration and improving safety in complex industrial tasks.
⚡ 2025 Highlight: Over 60% of first-time fixes in smart factories now rely on AR-guided workflows.
💡 Use Case: PTC Vuforia + Microsoft HoloLens for Field Support
Technology: AR headsets + Vuforia Studio
Application: Maintenance engineers view interactive AR overlays on complex machinery in real time.
Impact: Reduces errors and boosts first-time fix rates by up to 30%.
Social Value: Safer training and faster repairs with minimal human intervention in hazardous environments.
12. Additive Manufacturing (3D printing).
3D printing accelerates prototyping and customized production with minimal waste. Innovations in materials and printing speed are making it integral to industries like aerospace and automotive.
✅ Why it matters: enables fast, waste-reducing, on-demand production of complex, high-performance components..
🖥️ Trend: Additive manufacturing sees 40% growth, with aerospace and healthcare leading certified part production.
💡 Use Case: EOS 3D Printers + Siemens NX Additive Manufacturing
Technology: EOS M400 metal printers + Siemens design software
Application: Aerospace and medical parts are printed with complex geometries not possible through traditional methods.
Impact: Reduces part lead time by 70%, cuts material waste significantly.
Social Value: Speeds innovation and supports decentralization of supply chains — especially critical during global crises.
🚀 Conclusion: Staying Ahead in 2025
The industrial automation trends of 2025 reflect a broader movement toward intelligent, agile, and connected manufacturing. Whether you're a plant manager, systems engineer, or automation enthusiast, staying ahead of these trends will help you drive innovation, reduce costs, and future-proof your operations.
Innovation
Exploring technology, growth, and healthy lifestyles together.
Empowerment
Progress
© 2025. All rights reserved.
connection